About Pneumatic Products
PPC’s Heritage:
Since 1946, PPC has been recognized as the world’s largest manufacturer of compressed air purification equipment. PPC leads the industry in dehydration technology, system hardware, and support services. PPC has more patents granted and pending than any other dryer manufacturer. Based in Ocala, Florida PPC maintains a state-of-the-art desiccant dryer manufacturing facility.
PPC’s heritage has been built on a solid foundation of successfully solving the compressed air contamination problems of the most demanding industries including aerospace, food & beverage, chemical, biochemical, electronics, primary metals, power generation, petro-chemical, pulp & paper and other industrial applications.
PPC’s Engineered Components:
PPC’s unique approach to integrated system components allows for a system design that specifically meets your needs. Engineered Switching Valve & Energy Management components designed for the rigors of air dryer service provide the lowest life-cycle costs & optimized system performance.
PPC’s Proven Quality & Reliabity:
PPC is serving thousands upon thousands of customers with critical applications with an average of four PPC desiccant dryers per facility. Solving over 40% of the world’s critical compressed air contamination problems, PPC’s reputation for quality and reliability by design is un-matched in the industry.
No Application is Too Large or Too Small:
PPC manufactures engineered compressed air & gas purification equipment for flows of 2 scfm up to 15,000 scfm as standard product. Larger air & gas purification systems and custom designs are available upon request for almost any type of air or gas dehydration application.
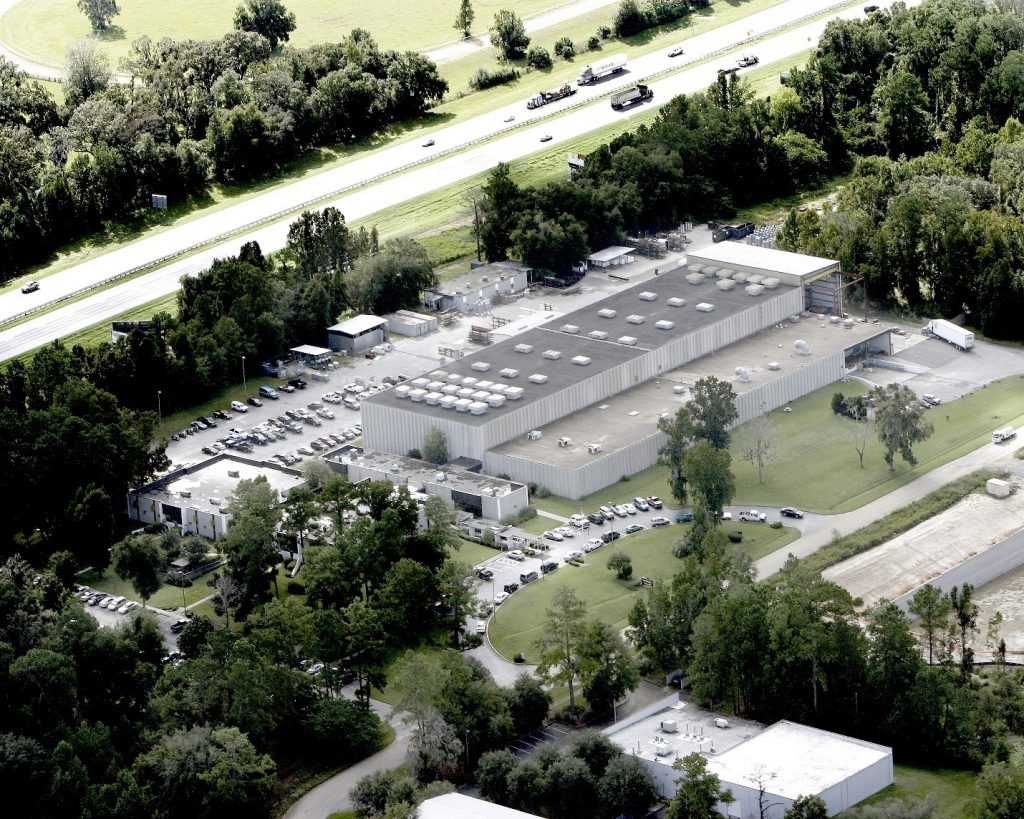
Arial view of SPX – PPC manufacturing facility in Ocala, Florida.
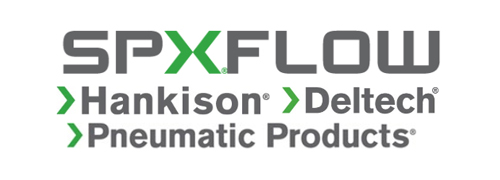
The DHA & CDA Series heatless desiccant air dryers have been designed to provide specified performance with unquestioned durability & reliable operation even in hostile environmental conditions. This design offers Switching Valves with at least a 5-year life to eliminate worries about maintenances or calibration.
- 30 to 1,600 scfm Flow Range
- Standard Operating Pressure up to 150 psig
- -40 and -100 Degrees F Outlet Pressure Dewpoint Available
- Downflow Drying Design to Eliminate Bed Fluidization for Extended Desiccant Media Life.
- ASME Coded Vessels with Corrosion Allowance
- Corrosion Resistant & Non-Lubricated Poppet-Style Valves with Stainless Steel Internals & Cycle Tested for Over 1,000,000 Cycles.
- AMLOC Energy Management System for Energy Savings at Part-Load Operation. Probe Calibration is Not Required and Includes a Lifetime Warranty!
- ADC SMarT Control System with Full System Diagnostic Capability. Control System Includes Ethernet Communication and RS-485 Connectivity Allowing the Controller to Communicate with ModBus applications.
- High Efficiency Prefilters & Afterfilters Included as Standard.
- More Information
CHA Series Heatless Air Dryers
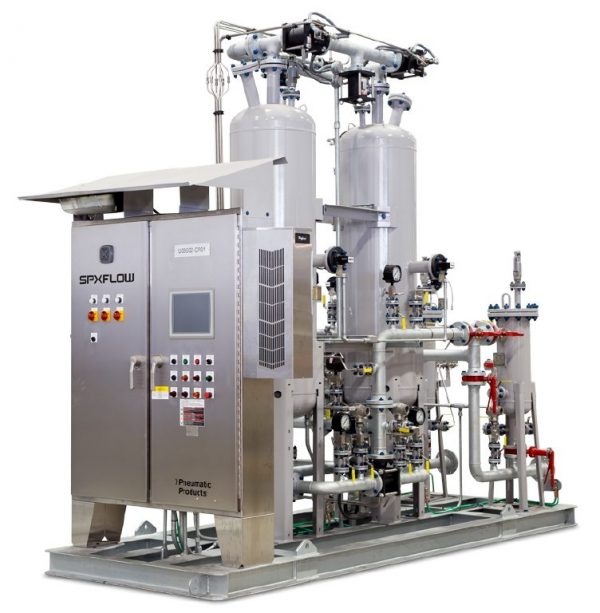
The CHA Series heatless desiccant air drying technology is the model of simplicity and reliability for large flow compressed air purification applications. CHA Series compressed air & gas dryers offer versatility of application and excel in hostile environments where corrosive, toxic, or explosive elements exist.
- 2,000 to 15,000 scfm Standard Flow Range
- Standard Operating Pressure up to 150 psig
- -40 and -100 Degrees F Outlet Pressure Dewpoint Available
- Downflow Drying Design to Eliminate Bed Fluidization for Extended Desiccant Media Life.
- ASME Coded Vessels with 1/16” Corrosion Allowance
- Century Series Corrosion Resistant & Non-Lubricated Poppet-Style Valves with Stainless Steel Internals & Cycle Tested to Over 500,000 Cycles.
- AMLOC Energy Management System for Energy Savings at Part-Load Operation. Probe Calibration is Not Required and Includes a Lifetime Warranty!
- ADC SMarT Control System with Full System Diagnostic Capability & Operational History. Control System Includes Ethernet Communication and RS-485 Connectivity Allowing the Controller to Communicate with ModBus applications.
- High Efficiency Prefilters & Afterfilters Included as Standard.
- More Information
- 1,200 to 13,000 scfm Standard Flow Range
- Standard Operating Pressure up to 150 psig
- -40 Degrees F Outlet Pressure Dewpoint Available
- Downflow Drying Design to Eliminate Bed Fluidization for Extended Desiccant Media Life.
- ASME Coded Vessels with 1/16” Corrosion Allowance
- Century Series Corrosion Resistant & Non-Lubricated Poppet-Style Valves with Stainless Steel Internals & Cycle Tested to Over 500,000 Cycles.
- AMLOC Energy Management System for Energy Savings at Part-Load Operation. Probe Calibration is Not Required and Includes a Lifetime Warranty!
- ADC SMarT Control System with Full System Diagnostic Capability & Operational History. Control System Includes Ethernet Communication and RS-485 Connectivity Allowing the Controller to Communicate with ModBus applications.
- High Efficiency Prefilters & Afterfilters Included as Standard.
- More Information
For superior efficiency, the DEA Series incorporates the finest components for maximum efficiency and reliability. The Downflow drying process coupled with the stored heat-of-adsorption and equi-distant desiccant bed heating provide the ultimate in Energy Efficiency. With the standard AMLOC Energy Management System, this highly efficient design averages less than 1% purge gas to assist with the regeneration process. DEA Series dryers approach 97% plus efficiency by design!
- 330 to 4,300 scfm Standard Flow Range
- Standard Operating Pressure up to 150 psig
- -40 Degrees F Outlet Pressure Dewpoint Available
- Downflow Drying Design to Eliminate Bed Fluidization for Extended Desiccant Media Life.
- ASME Coded Vessels with 1/16” Corrosion Allowance
- Century Series Corrosion Resistant & Non-Lubricated Poppet-Style Valves with Stainless Steel Internals & Cycle Tested to Over 500,000 Cycles.
- AMLOC Energy Management System for Energy Savings at Part-Load Operation. Probe Calibration is Not Required and Includes a Lifetime Warranty!
- ADC SMarT Control System with Full System Diagnostic Capability & Operational History. Control System Includes Ethernet Communication and RS-485 Connectivity Allowing the Controller to Communicate with ModBus applications.
- High Efficiency Prefilters & Afterfilters Included as Standard.
- More Information
NRG-LES Series Heat-of-Compression Air Dryers
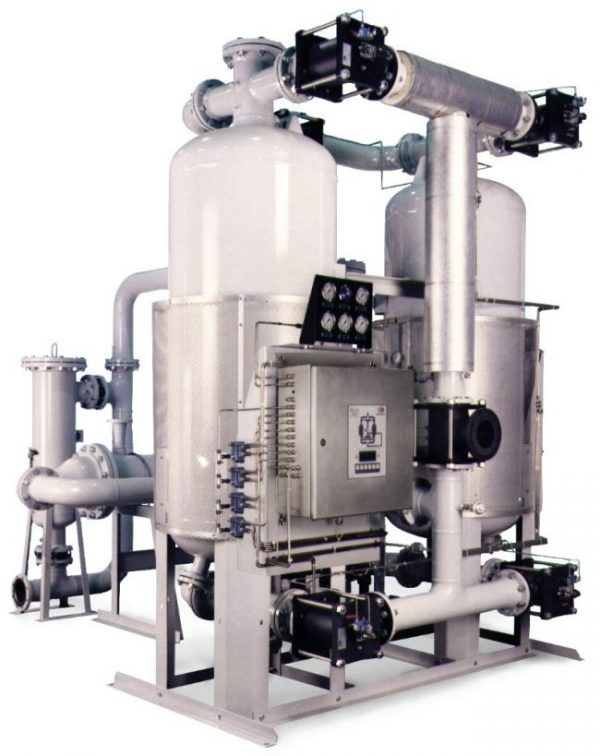
Pneumatic Product’s NRG-LES Heat-of-Compression desiccant air dryers provide a cost-effective solution to remove moisture from compressed air. Thermal energy generated during the air compression process is utilized to regenerate the off-line desiccant bed. Ideally suited for Oil-Free compressors, the NGG-LES dryer turns waste heat from the compressor into energy savings!
- 350 to 10,000 scfm Standard Flow Range in 18 Models
- Standard Operating Pressure up to 150 psig
- Delivers ISO 8573:1 Class 2 to 4 Outlet Pressure Dewpoint Performance
- No Purge Gas or Heaters Required – Less Than $50 A Year to Operate!
- High Efficiency 316 Stainless Steel Aftercooler Included
- ASME Coded Vessels Built to Section VIII, Division 1
- Models 350-450 scfm utilize Y-Angle Poppet Valves. Models 600 to 10000 scfm utilize High-Performance Butterfly Valves with Double Action Actuators & Valve Position Indicators.
- Energy Management System available for extending the drying cycle to compensate for changes in operating conditions.
- NRG-LES Control System with Full System Diagnostic Capability & Operational History.
- High Temperature Afterfilter Included.
- More Information
Engineering & Support Services
Your Needs:
Today’s competitive manufacturing environment requires that compressed air & gas purification systems perform to your specification with the lowest possible life-cycle costs and minimum downtime. At PPC our main objective is to maximize your return on investment in our air & gas purification systems.
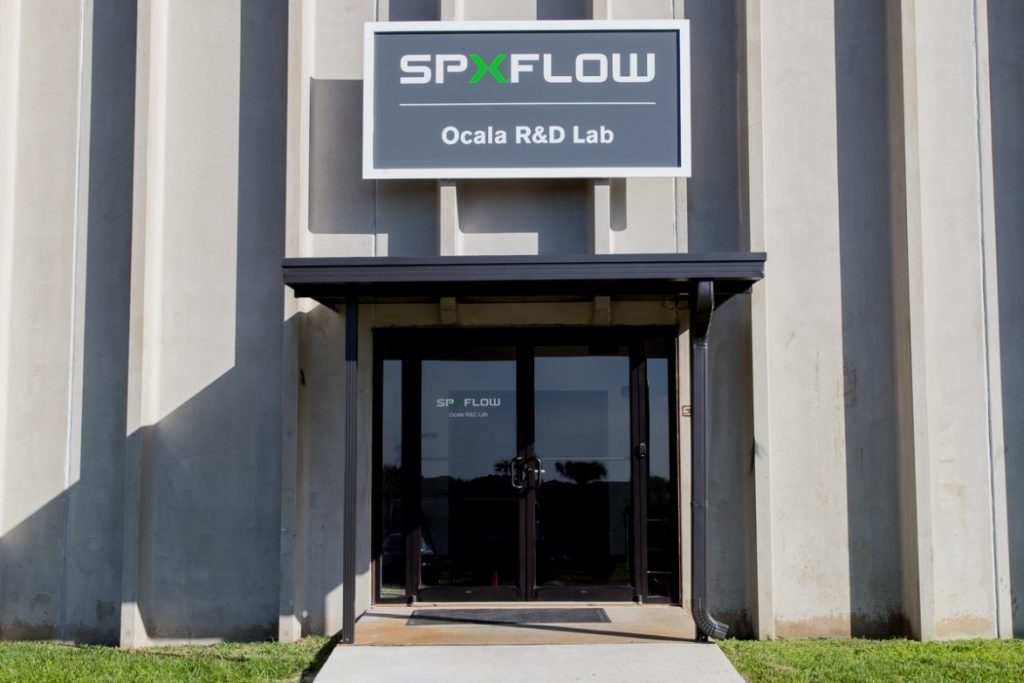
SPX Flow Research and Development lab.
PPC’s Commitment to Our Customers:
To achieve our goal of maximizing your return on investment in our products, a comprehensive Engineering and Service organization is necessary. PPC is pleased to offer the following services:
Engineering Services:
- R & D Services for Unique Applications & Contamination Problems.
- In-House Engineering for System Design & Layout.
- Factory Trained Application Engineers & Consultants.
- In Plant Inspections, Surveys, and Monitoring.
- On-Site Technical Seminars
- Factory Seminars at our World Class Training Center in Ocala, Florida
Field Services:
- Factory Authorized Service Centers Worldwide.
- Factory Trained and Certified Service Technicians.
- State of the Art Service Management and Scheduling Systems.
- Local Stocking Service Centers Backed by our National Parts Distribution Center in Ocala, Florida.
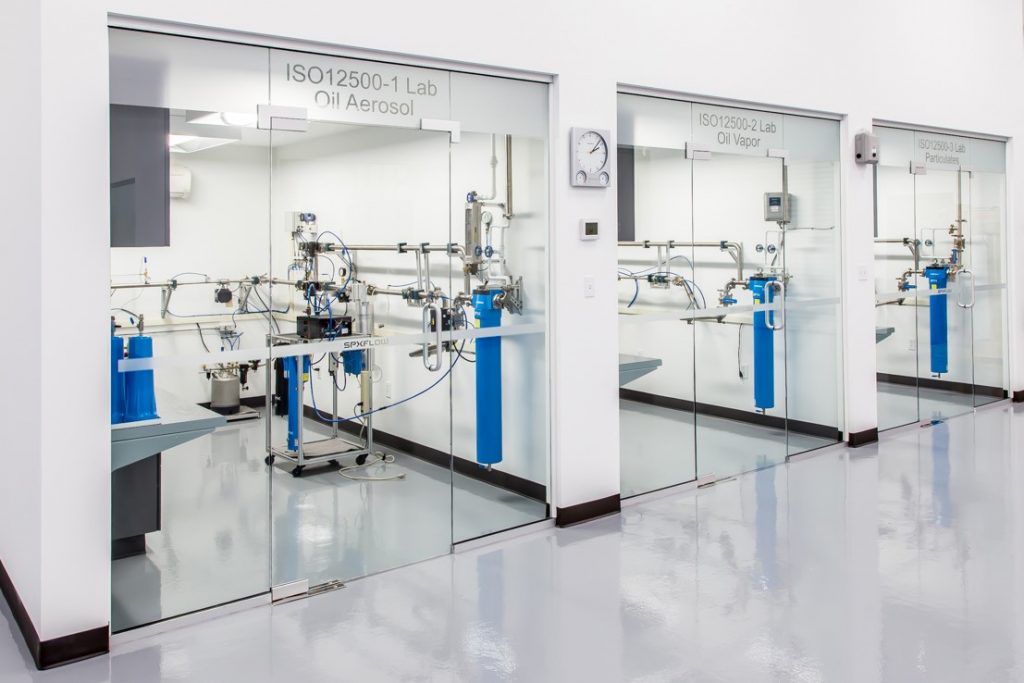
SPX Flow PPC Lab & Testing Facility.