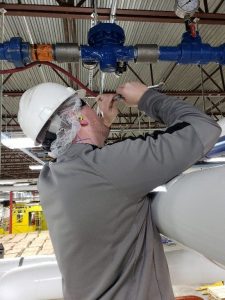
What size air compressor does our facility need? How much is our company spending to operate our compressed air system? If you’ve asked these questions in the past, you’re not alone. These are some of the most common questions large manufacturing facility operators face, typically followed by another: Can we reduce the cost of our energy expenses?
The key to answering these questions lies in a simple step that you might have overlooked: a compressed air audit. A compressed air audit will not only provide the answers, but when performed by experts in the field, it can yield major energy savings. That’s right, a compressed air audit is the first step in putting money back into your company’s bottom line.
COMPRESSED AIR AUDITS GIVE YOU A LOT OF INFORMATION
A compressed air audit comes in two main forms. To put it simply, the basics are grounded in supply and demand. While it sounds like the catch phrase from your high school economics class, measuring your air supply and air production demand is the staple in mapping out your energy expenditure and finding ways to improve that number.
A complete air audit will expose how you are using your air, how it can be improved, how the air compressors you have are working within your system, and how much energy is being spent or wasted in the process.
WHAT DO YOU DO WITH ALL THAT INFO?
Information provided by an audit gives you the opportunity to eliminate inefficient uses of your compressed air. This means you can save money and energy by identifying areas that throw your air to waste – and set measures in place that will advance your air efficiency.
Introducing compressor automation is a simple example of this payoff. Not only will it ensure that you have air when you need it, it will systematize the process and provide the right amount of air by detecting your facility’s air requirement at any given time. Automation of your compressed air system will provide stable air pressure and create consistency in your processes, increasing your throughput and reducing scrap air.
Consider this: a facility with a 400 hp compressor was previously spending $154,903 per year in compressed air energy. After their air audit, Blake & Pendleton’s compressed air specialists used the information provided to reduce that number to $97,109. That’s a savings of $57,794 – or 37 percent – just in compressed air operation expenses. That’s more than just a scratch on the surface!
A compressed air audit will lay out exactly how much it’s costing at your facility, and a compressed air expert will use that information to determine what can be changed to get that cost down.
WHO DO YOU CONTACT FOR A COMPRESSED AIR AUDIT?
Blake & Pendleton’s team of experts are well-versed in the compressed air auditing process. Your nearest Blake & Pendleton Area Manager will coordinate the ins and outs of an audit for you; working closely with you to establish the most efficient way to minimize the cost of operating your compressed air system.
To find out how to get started, contact our team!