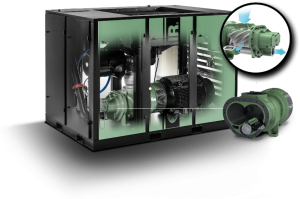
When it comes to air capacity control, there’s no shortage of options on the table. But when deciding what your best fit is, there’s only one consideration: efficiency.
What control system will offer you the best outcome while costing you the least to operate? The answer can be found in Sullair’s Electronic Spiral Valve. But to understand the why, you’ve got to understand the how.
BREIF HISTORY OF CAPACITY CONTROL METHODS
In oil flooded compressor infancy, most manufacturers opted for load/no-load air capacity control. While this method can be efficient in some circumstances, it requires a pressure band that often pushes higher pressure than you need and thus gives inconsistent pressure flow. In essence, it costs you money for pressure that’s higher than you actually need, while incapable of providing the exact air flow that you require.
With the shortcomings of a load/un-load control method in mind, many compressed air users turned to an inlet modulation arrangement. Inlet modulation chokes the inlet down to the necessary air requirement, which soundly eliminates the need for a pressure band.
But while inlet choking solved one problem, it presented several new ones. The most glaring issue of inlet modulation is a potentially large waste of power. With this method, 70% capacity still requires using 91% of the compressor’s maximum power. That’s a huge disparity that results in throwing a lot of money to the wind (or, to the air if you want to be specific).
THEN CAME THE ANSWER…MAYBE
The solution to capacity control came in the form of the Variable Frequency Drives (VFD/VSD). VFD introduced a highly efficient way to control air capacity output by changing the speed of the compressor to match system demand. VFD finally eliminated the issues of requiring a pressure band and wasting power, all while providing stable and reliable air pressure.
But, as with capacity control methods before it, VFD also comes with a downside. Though setting the standards in efficiency, the frequency drives are expensive, finicky, necessitate environmental control, and often require expensive part replacements. These factors unfortunately mean that VFD doesn’t fit the criteria for many compressed air users.
INTRODUCING THE SPIRAL VALVE
In 1984, Sullair introduced the game-changing Spiral Valve. Differing from all other capacity control systems, the Spiral Valve allowed shortening the rotor length to match the air demand instead of changing the compressor speed.
Basically, the Spiral Valve makes the airend effectively smaller and therefore puts out less air.
BUT, WAIT, THE SPIRAL VALVE GOT EVEN BETTER
Building on their earlier Spiral Valve technology, Sullair has now introduced an electronic version of the Spiral Valve. And this design changes everything for compressed air users.
The Electronic Spiral Valve technology checks all the boxes of air capacity control. It holds a set pressure, is only marginally more expensive than a standard machine, and achieves very close to the efficiency of a VFD without any of the associated problems.
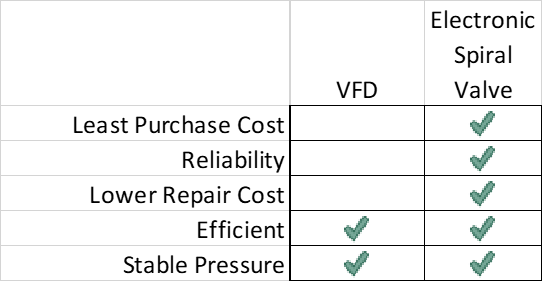
Unique to Sullair, the Electronic Spiral Valve technology is available from 125-200 HP units in Sullair’s popular LS Series.
To learn more about the Electronic Spiral Valve technology or for an evaluation of your compressor needs, contact Blake & Pendleton and we’ll help you reach your full compressed air potential.