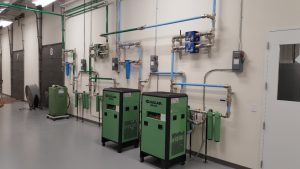
So, you’ve got water in your compressed air lines.
Water collection is a common issue at many facilities. If left untreated, the water can cause rust to build up on valves, damaging expensive equipment and compromising your compressed air quality.
To correct it, and to prevent recurring water issues, it’s important to understand where all that water is coming from.
When air is pulled into a compressor system from the surrounding environment, moisture that is naturally in the atmosphere is carried through the system. Without a proper method of removing the moisture, water begins to collect at the low points in the air lines. If you don’t have an aftercooler and drains, that moisture continues in the pipe to your air system and your process equipment. A 50-horsepower compressor can put up to 18 gallons of water into your system every 24 hours! That’s a lot of water.
Focusing on the Basics is How You Get Your Air System Back in Shape
To get your air system back into good shape, you will need to go back to the basics. The first step is to make sure that your air compressor is serviced properly and not running hot. Increased temperatures allow more water to condense as the air cools in your system, which could account for a majority of your water collection.
The next step is to check all drain valves and make sure they are working properly. Drain valve checks should be performed daily to help identify potential issues as soon as they appear. If you need new drain valves, we recommend no-loss drains to help make your air systems more efficient.
Other Potential Issues Hindering the Efficiency of Your Air System
If the temperature and drain valves look good, your compressed air dryer is the main suspect. Responsible for lowering the dewpoint to prevent water reappearance post-aftercooler, compressed air dryers play an important role in your processing and efficiency. While they typically do their jobs quietly, they do require regular maintenance to keep them in check.
Refrigerated dryers are particularly susceptible to dirty condensers, bad drains, defective hot gas by-pass valves, and other mechanical issues. In the event you need a new refrigerated dryer, have a Blake and Pendleton Area Manager review your system to make sure you are getting the correct dryer for your system demands.
For more sensitive process equipment, like those used in pharmaceuticals, electronics, and chemical processes, you may need a desiccant dryer. We offer a broad range of desiccant dryers to meet system requirements from 0°F to -100°F dew points. Like refrigerated dryers, it will be critical to your operations to keep them maintained and serviced regularly.
While there’s not a one-size-fits-all solution to water in your air lines, regular equipment maintenance and a properly selected compressed air dryer will help correct and prevent water issues. Call Blake and Pendleton at (800) 333-6650 and we can ensure that you stay ahead of moisture damage and optimize your compressed air production.